photoresist හි ආලේපන ක්රම සාමාන්යයෙන් Spin coating, dip coating සහ roll coating ලෙස බෙදී ඇති අතර ඒ අතරින් Spin coating බහුලව භාවිතා වේ. භ්රමණය වන ආලේපනය මගින් උපස්ථරය මත photoresist බිංදු දමන අතර, උපස්ථරය අධික වේගයෙන් කරකවා ප්රභාරසිස්ට් පටලයක් ලබා ගත හැක. ඊට පසු, උණුසුම් තට්ටුවක් මත රත් කිරීමෙන් ඝන චිත්රපටයක් ලබා ගත හැකිය. අති තුනී පටල (20nm පමණ) සිට 100um පමණ ඝන පටල දක්වා ආෙල්පනය කිරීම සඳහා Spin coating සුදුසු වේ. එහි ලක්ෂණ වන්නේ හොඳ ඒකාකාරිත්වය, වේෆර් අතර ඒකාකාර පටල ඝනකම, අඩුපාඩු කිහිපයක්, ආදිය සහ ඉහළ ආලේපන කාර්ය සාධනයක් සහිත චිත්රපටයක් ලබා ගත හැකිය.
ස්පින් ආලේපන ක්රියාවලිය
භ්රමණය වන ආලේපනය අතරතුර, උපස්ථරයේ ප්රධාන භ්රමණ වේගය ෆොටෝරෙස්ට්රයේ පටල ඝණකම තීරණය කරයි. භ්රමණ වේගය සහ චිත්රපට ඝණකම අතර සම්බන්ධය පහත පරිදි වේ:
Spin=kTn
සූත්රයේ, Spin යනු භ්රමණ වේගයයි; T යනු පටල ඝණකම; k සහ n නියත වේ.
කැරකෙන ආලේපන ක්රියාවලියට බලපාන සාධක
චිත්රපට ඝනකම ප්රධාන භ්රමණ වේගය අනුව තීරණය වුවද, එය කාමර උෂ්ණත්වය, ආර්ද්රතාවය, ප්රකාශන දුස්ස්රාවීතාවය සහ ප්රභා ප්රතිරෝධී වර්ගයට ද සම්බන්ධ වේ. විවිධ වර්ගයේ ෆොටෝරෙස්ට් ආලේපන වක්ර සංසන්දනය කිරීම රූප සටහන 1 හි දැක්වේ.
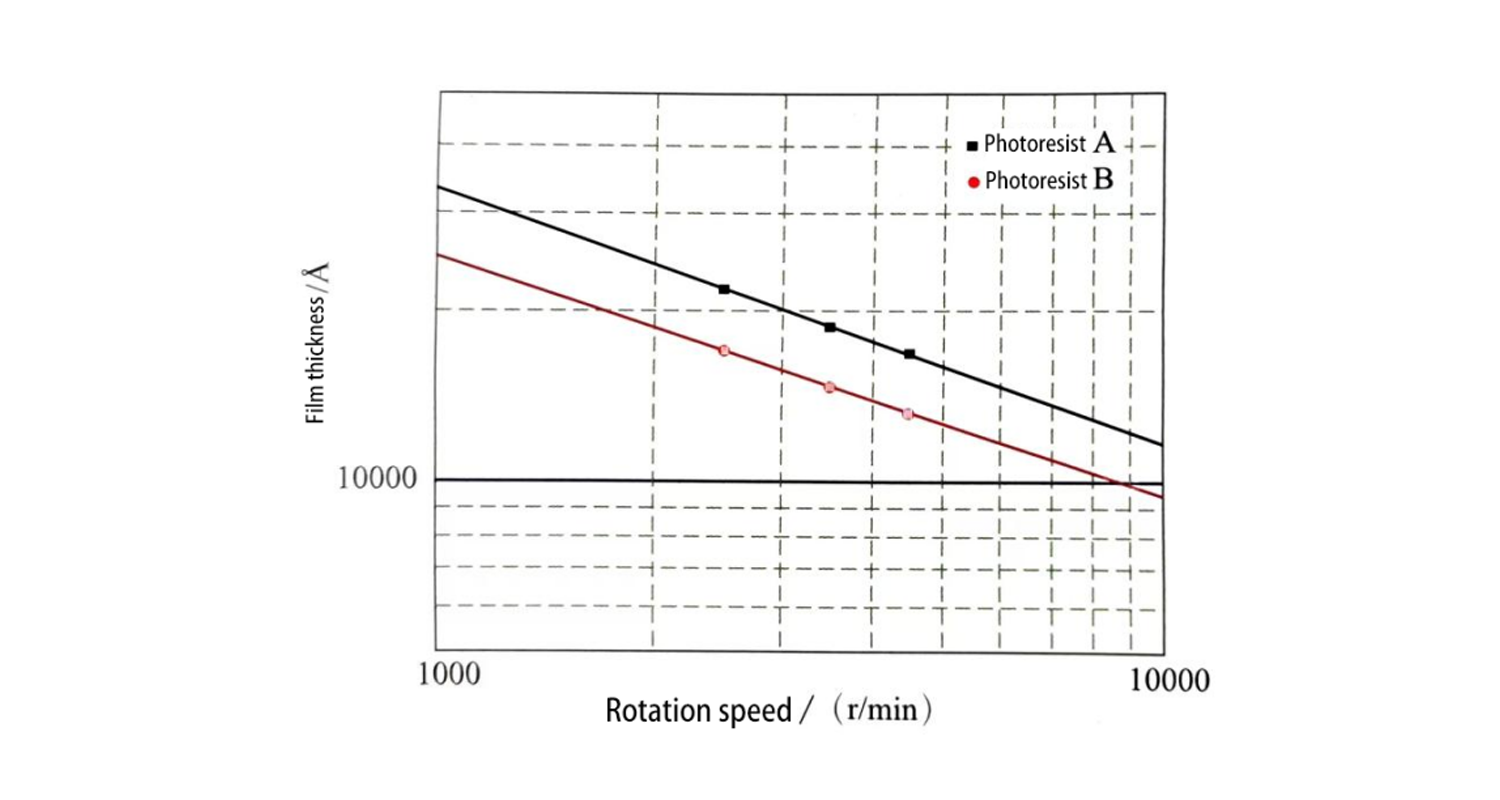
රූපය 1: විවිධ වර්ගයේ ෆොටෝරෙස්ට් ආලේපන වක්ර සංසන්දනය කිරීම
ප්රධාන භ්රමණ කාලයෙහි බලපෑම
ප්රධාන භ්රමණ කාලය කෙටි වන තරමට චිත්රපටයේ ඝනකම ඝනකම වැඩි වේ. ප්රධාන භ්රමණ කාලය වැඩි වන විට, චිත්රපටය තුනී වේ. එය තත්පර 20 ඉක්මවන විට, චිත්රපට ඝනකම පාහේ නොවෙනස්ව පවතී. එමනිසා, ප්රධාන භ්රමණ කාලය සාමාන්යයෙන් තත්පර 20 කට වඩා වැඩි කාලයක් තෝරා ගනු ලැබේ. ප්රධාන භ්රමණ කාලය සහ චිත්රපට ඝණකම අතර සම්බන්ධය රූප සටහන 2 හි දැක්වේ.
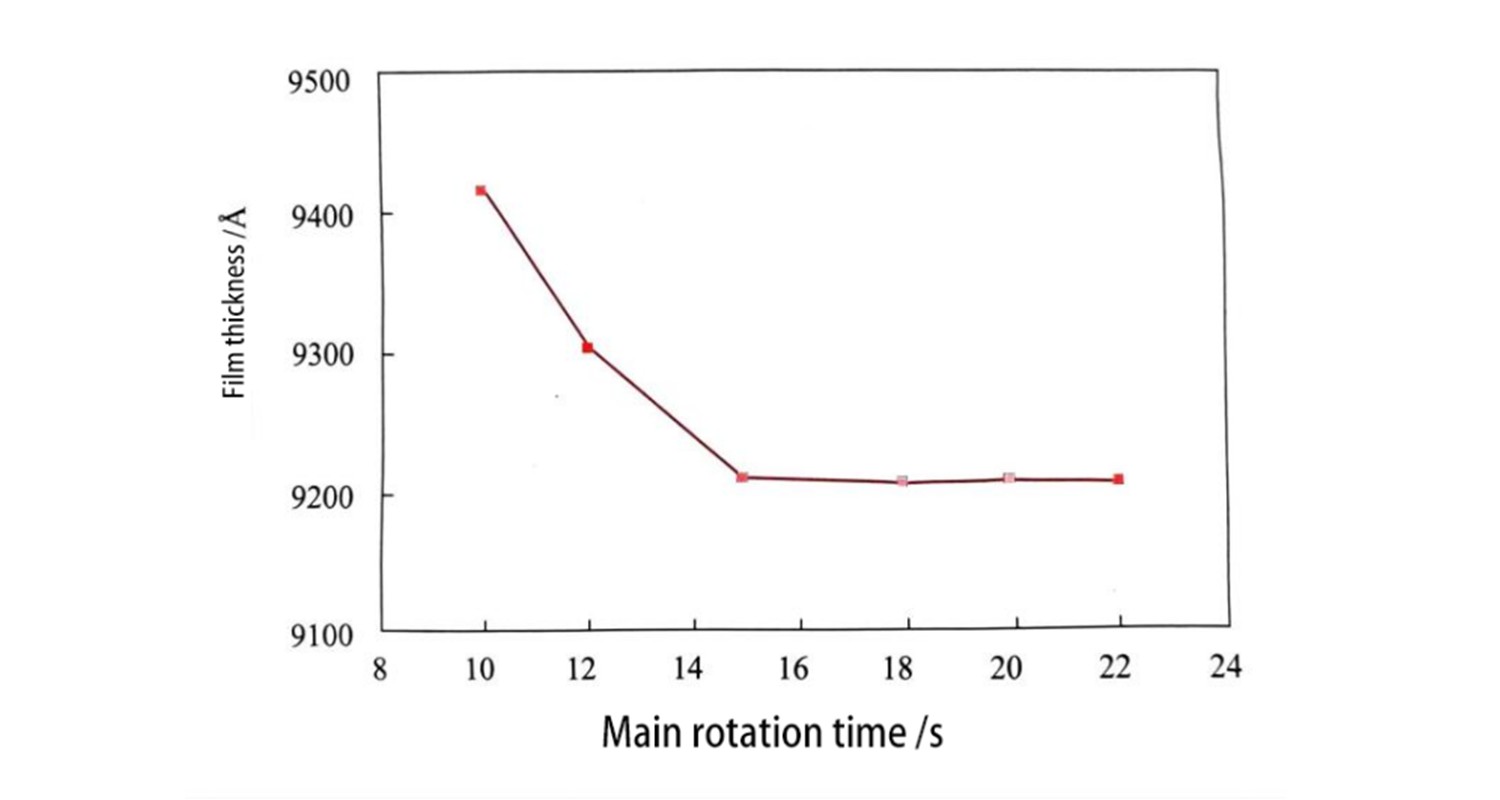
රූපය 2: ප්රධාන භ්රමණ කාලය සහ චිත්රපට ඝණකම අතර සම්බන්ධය
ඡායාරූප ප්රතිරෝධකය උපස්ථරය මතට පතිත වූ විට, පසුව ඇති ප්රධාන භ්රමණ වේගය සමාන වුවද, ජල බිඳිති අතරතුර උපස්ථරයේ භ්රමණ වේගය අවසාන පටල ඝණත්වයට බලපානු ඇත. ජල බිඳිති අතරතුර උපස්ථර භ්රමණ වේගය වැඩි වීමත් සමඟ ප්රභා ප්රතිරෝධක චිත්රපටයේ ඝනකම වැඩි වේ, එය ජල බිඳිති වලින් පසුව දිග හැරෙන විට ද්රාවක වාෂ්පීකරණයේ බලපෑම නිසාය. රූප සටහන 3 ෆොටෝරෙස්ට් බිංදු අතරතුර විවිධ උපස්ථර භ්රමණ වේගයන්හි චිත්රපට ඝණකම සහ ප්රධාන භ්රමණ වේගය අතර සම්බන්ධය පෙන්වයි. බිංදු උපස්ථරයේ භ්රමණ වේගය වැඩි වීමත් සමඟ චිත්රපට ඝනකම වේගයෙන් වෙනස් වන අතර ප්රධාන භ්රමණ වේගය අඩු ප්රදේශයේ වෙනස වඩාත් පැහැදිලිව පෙනෙන බව රූපයෙන් පෙනේ.
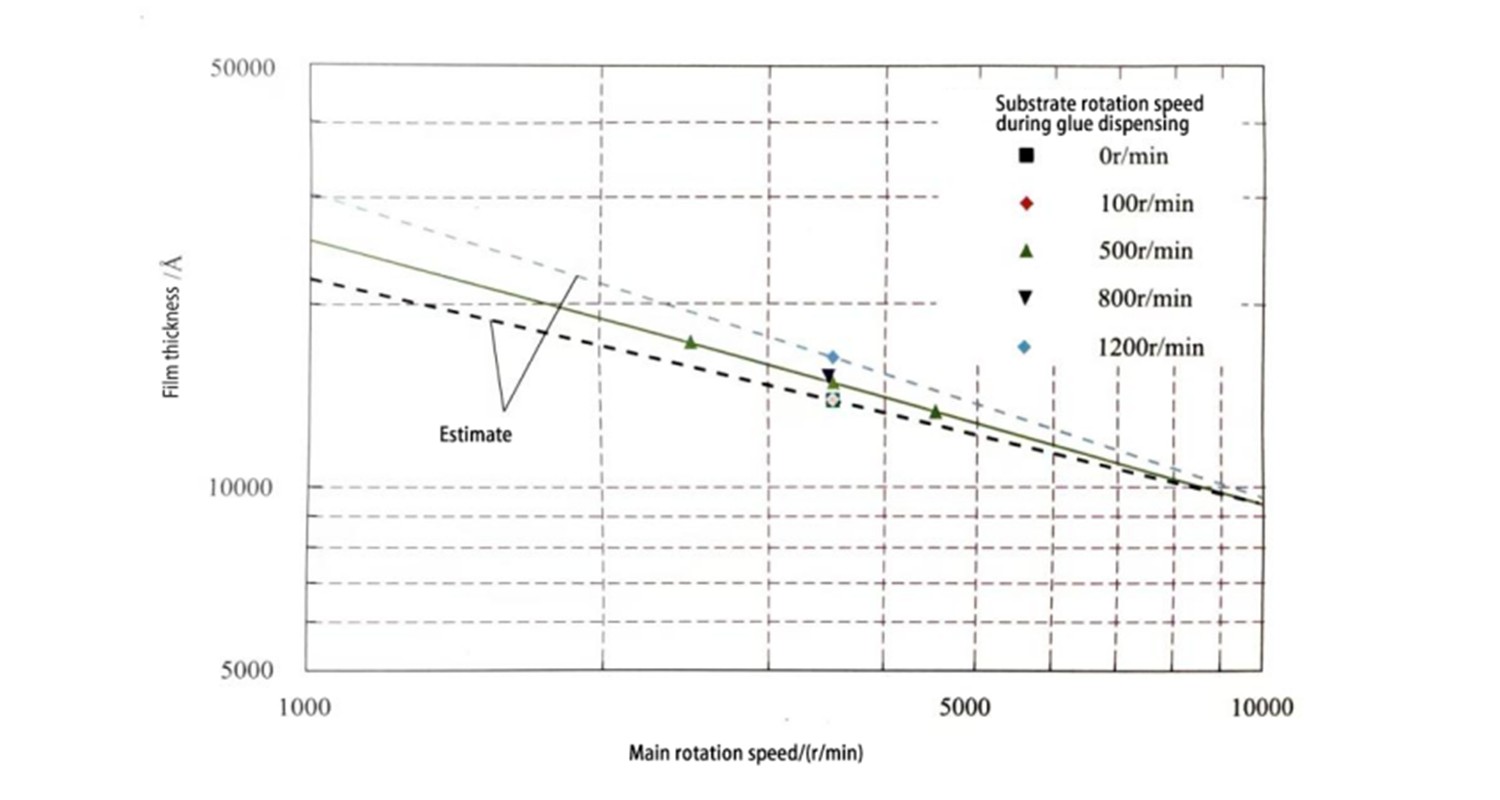
රූප සටහන 3: ප්රභා ප්රතිරෝධක බෙදා හැරීමේදී විවිධ උපස්ථර භ්රමණ වේගයන්හි චිත්රපට ඝණකම සහ ප්රධාන භ්රමණ වේගය අතර සම්බන්ධය
ආලේපනය තුළ ආර්ද්රතාවයේ බලපෑම
ආර්ද්රතාවය අඩු වන විට, චිත්රපට ඝනකම වැඩි වේ, ආර්ද්රතාවය අඩු වීම ද්රාවණයේ වාෂ්පීකරණය ප්රවර්ධනය කරයි. කෙසේ වෙතත්, චිත්රපට ඝණකම ව්යාප්තිය සැලකිය යුතු ලෙස වෙනස් නොවේ. රූප සටහන 4 ආෙල්පනය තුළ ආර්ද්රතාවය සහ පටල ඝණකම බෙදා හැරීම අතර සම්බන්ධය පෙන්වයි.
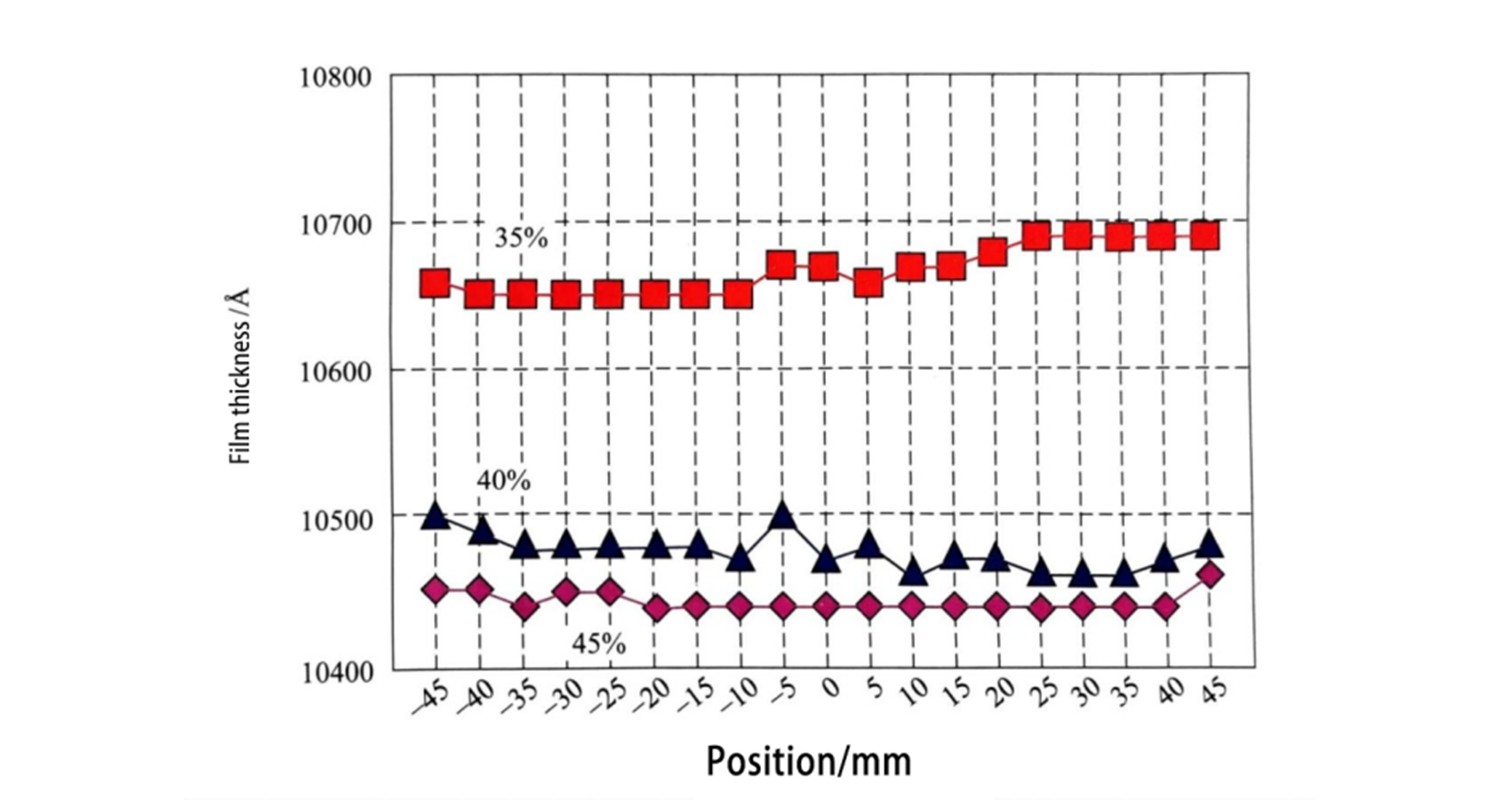
රූප සටහන 4: ආෙල්පනය තුළ ආර්ද්රතාවය සහ පටල ඝණකම බෙදා හැරීම අතර සම්බන්ධය
ආලේපනය තුළ උෂ්ණත්වයේ බලපෑම
ගෘහස්ථ උෂ්ණත්වය ඉහළ යන විට, චිත්රපටය ඝනකම වැඩි වේ. ඡායා රූප ප්රතිරෝධක පටල ඝණත්වය ව්යාප්තිය උත්තල සිට අවතල දක්වා වෙනස් වන බව රූප සටහන 5 මගින් දැක ගත හැක. රූපයේ ඇති වක්රය මඟින් ගෘහස්ථ උෂ්ණත්වය සෙල්සියස් අංශක 26 ක් වන අතර ප්රභා ප්රතිරෝධක උෂ්ණත්වය සෙල්සියස් අංශක 21 ක් වන විට ඉහළම ඒකාකාරිත්වය ලැබෙන බව පෙන්වයි.
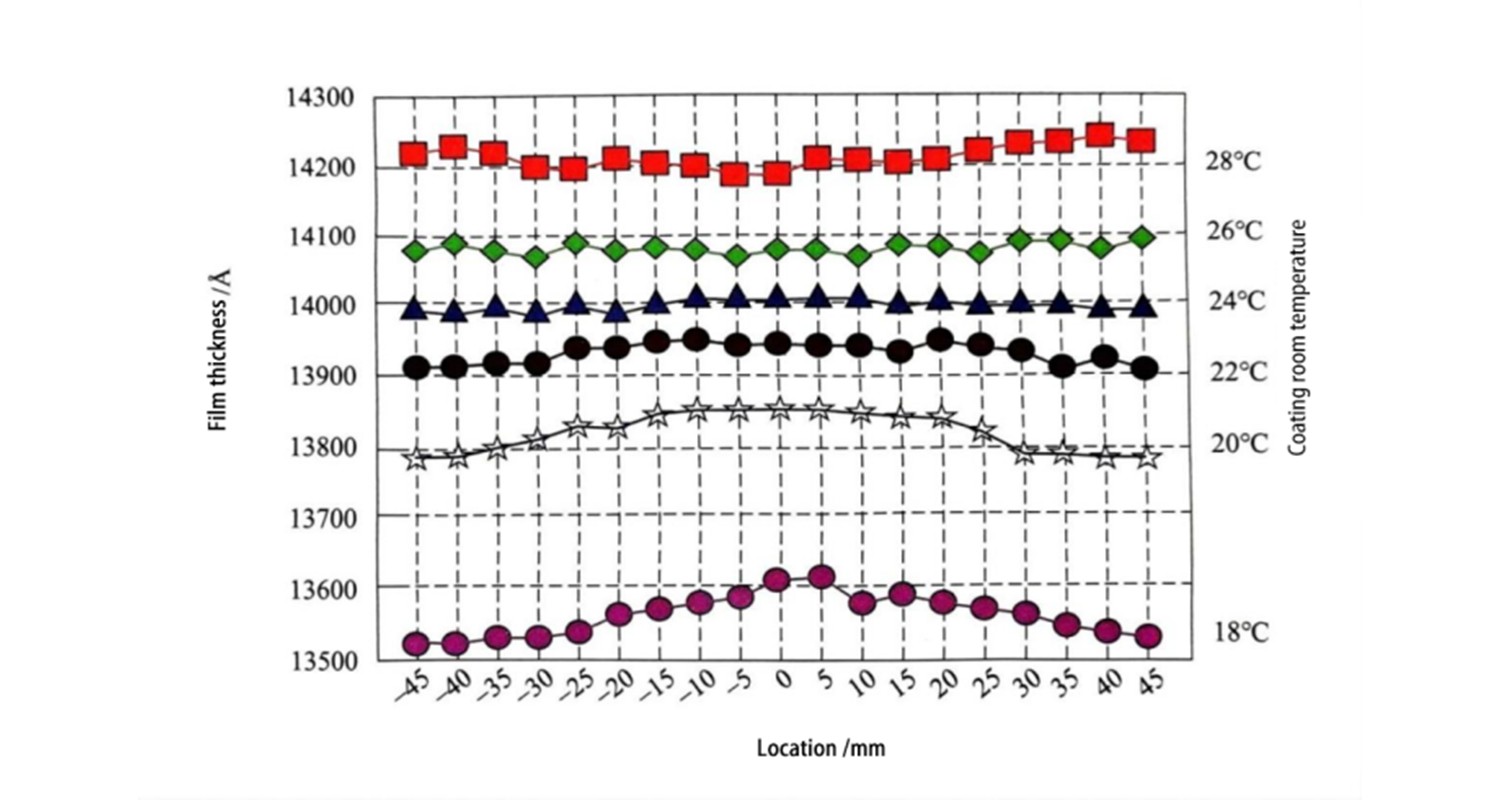
රූප සටහන 5: ආලේපනය අතරතුර උෂ්ණත්වය සහ පටල ඝණකම බෙදා හැරීම අතර සම්බන්ධතාවය
ආලේපනය තුළ පිටාර වේගයේ බලපෑම
රූප සටහන 6 මඟින් පිටාර වේගය සහ පටල ඝනකම ව්යාප්තිය අතර සම්බන්ධය පෙන්වයි. පිටාර ගැලීම නොමැති විට, වේෆරයේ කේන්ද්රය ඝන වීමට නැඹුරු වන බව පෙන්නුම් කරයි. පිටවන වේගය වැඩි කිරීමෙන් ඒකාකාරී බව වැඩි වේ, නමුත් එය ඕනෑවට වඩා වැඩි කළහොත්, ඒකාකාරී බව අඩු වේ. පිටාර වේගය සඳහා ප්රශස්ත අගයක් ඇති බව දැකිය හැකිය.
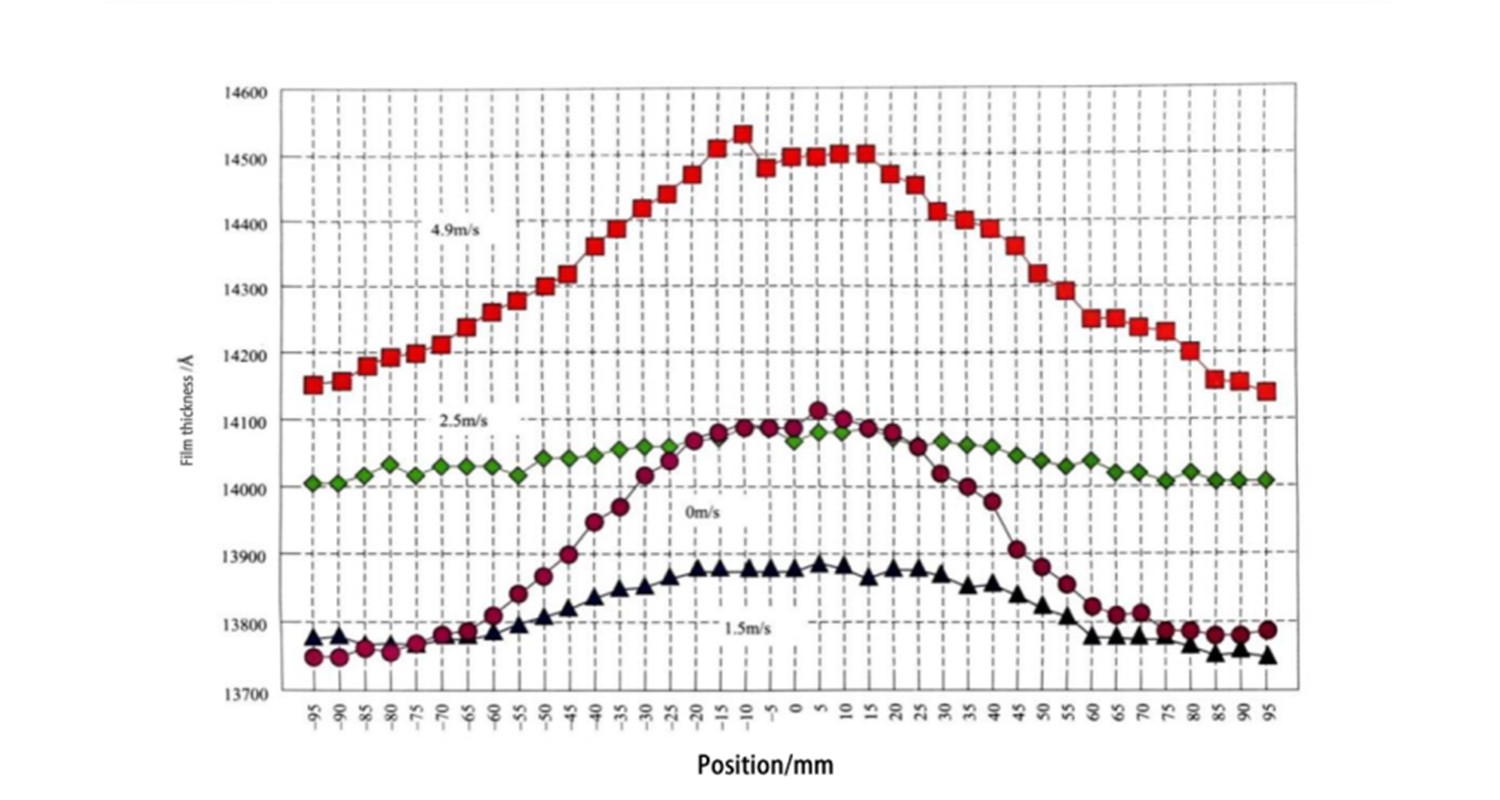
රූපය 6: පිටාර වේගය සහ පටල ඝනකම ව්යාප්තිය අතර සම්බන්ධය
HMDS ප්රතිකාරය
ප්රභා ප්රතිරෝධය වඩාත් ආලේප කළ හැකි බවට පත් කිරීම සඳහා, වේෆරය හෙක්සමෙතිල්ඩිසිලසාන් (HMDS) සමඟ ප්රතිකාර කිරීම අවශ්ය වේ. විශේෂයෙන්ම Si ඔක්සයිඩ් චිත්රපටයේ මතුපිටට තෙතමනය සවි කර ඇති විට, silanol සෑදී ඇත, එය photoresist හි ඇලවීම අඩු කරයි. තෙතමනය ඉවත් කිරීම සහ සිලැනෝල් දිරාපත් කිරීම සඳහා, වේෆර් සාමාන්යයෙන් 100-120 ° C දක්වා රත් කරනු ලබන අතර, රසායනික ප්රතික්රියාවක් ඇති කිරීම සඳහා මීදුම HMDS හඳුන්වා දෙනු ලැබේ. ප්රතික්රියා යාන්ත්රණය රූප සටහන 7 හි පෙන්වා ඇත. HMDS ප්රතිකාරය හරහා කුඩා ස්පර්ශක කෝණයක් සහිත ජලභීතික පෘෂ්ඨය විශාල ස්පර්ශක කෝණයක් සහිත ජලභීතික පෘෂ්ඨයක් බවට පත්වේ. වේෆර් රත් කිරීමෙන් ඉහළ ප්රභා ප්රතිරෝධක ඇලීමක් ලබා ගත හැක.
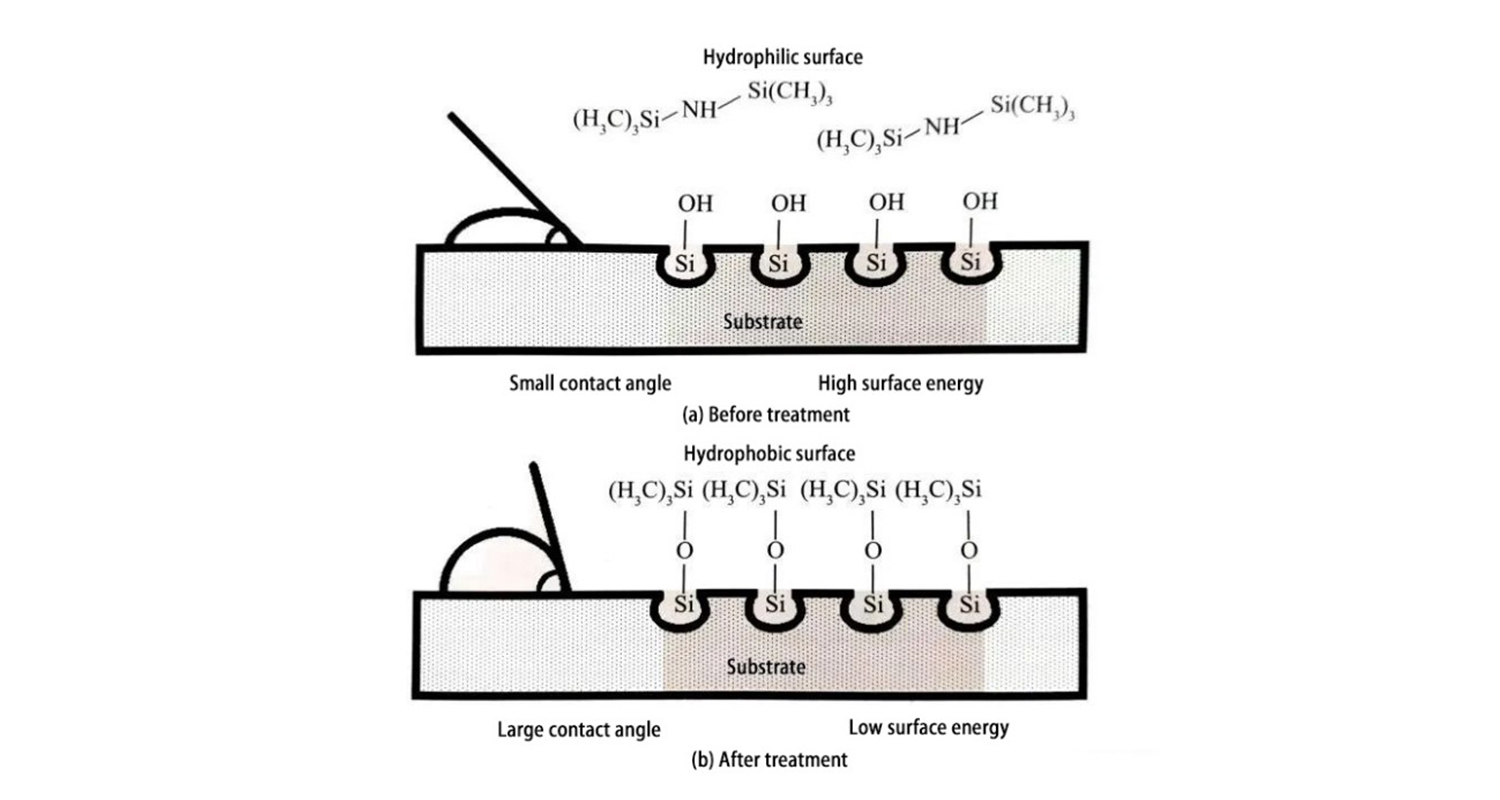
රූපය 7: HMDS ප්රතික්රියා යාන්ත්රණය
ස්පර්ශක කෝණය මැනීමෙන් HMDS ප්රතිකාරයේ බලපෑම නිරීක්ෂණය කළ හැක. HMDS ප්රතිකාර කාලය සහ සම්බන්ධතා කෝණය (ප්රතිකාර උෂ්ණත්වය 110 ° C) අතර සම්බන්ධය රූප සටහන 8 පෙන්වයි. උපස්ථරය Si වේ, HMDS ප්රතිකාර කාලය මිනිත්තු 1 ට වඩා වැඩි වේ, සම්බන්ධතා කෝණය 80 ° ට වඩා වැඩි වන අතර ප්රතිකාර බලපෑම ස්ථායී වේ. HMDS ප්රතිකාර උෂ්ණත්වය සහ ස්පර්ශක කෝණය (ප්රතිකාර කාලය 60s) අතර සම්බන්ධය රූප සටහන 9 පෙන්වයි. උෂ්ණත්වය 120℃ ඉක්මවන විට, ස්පර්ශක කෝණය අඩු වන අතර, තාපය හේතුවෙන් HMDS දිරාපත් වන බව පෙන්නුම් කරයි. එබැවින්, HMDS ප්රතිකාරය සාමාන්යයෙන් 100-110℃ දී සිදු කරනු ලැබේ.
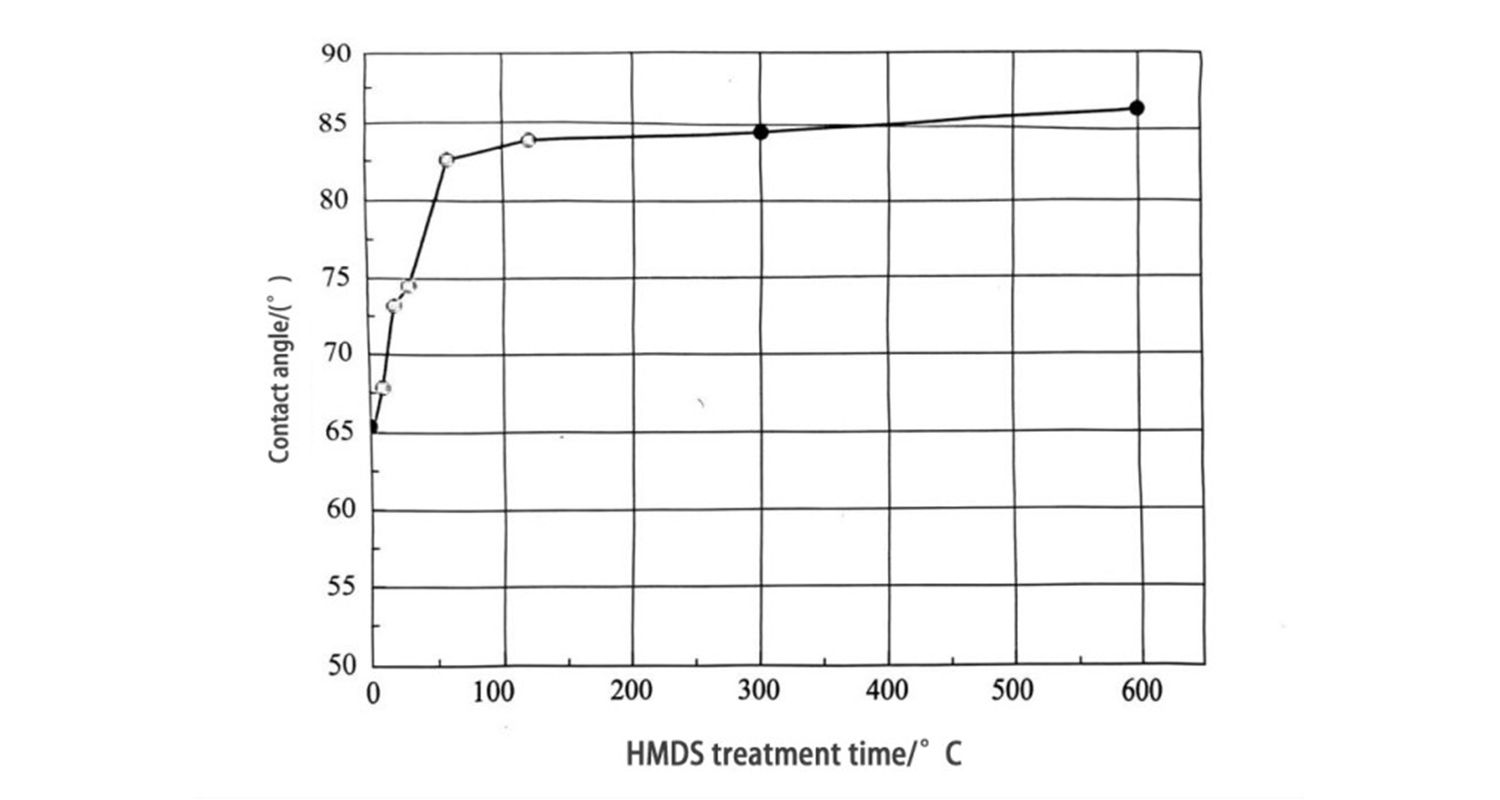
රූපය 8: HMDS ප්රතිකාර කාලය අතර සම්බන්ධතාවය
සහ සම්බන්ධතා කෝණය (ප්රතිකාර උෂ්ණත්වය 110℃)
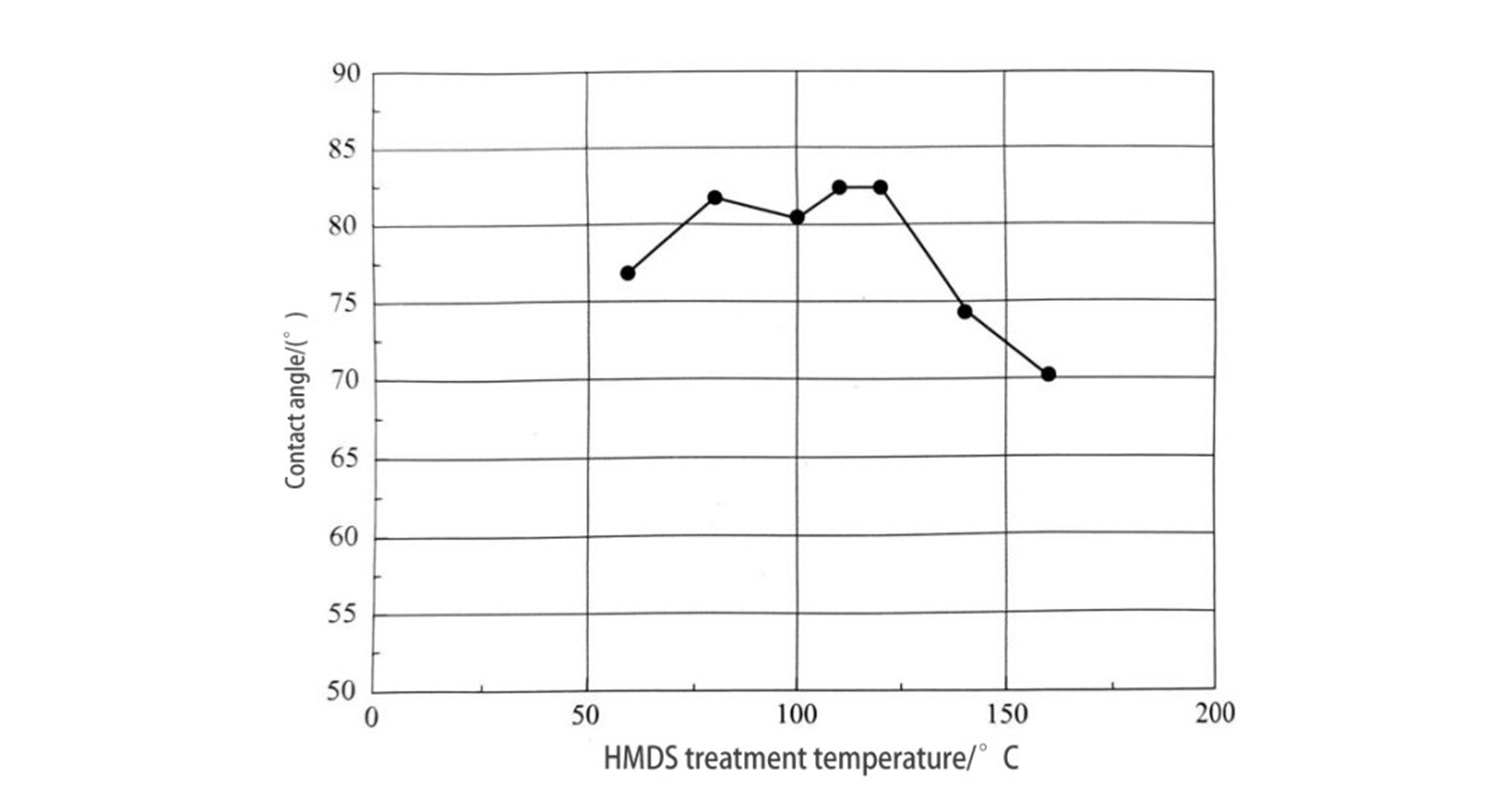
රූපය 9: HMDS ප්රතිකාර උෂ්ණත්වය සහ සම්බන්ධතා කෝණය අතර සම්බන්ධතාවය (ප්රතිකාර කාලය තත්පර 60)
HMDS ප්රතිකාරය ඔක්සයිඩ් පටලයක් සහිත සිලිකන් උපස්ථරයක් මත ඡායාරූප ප්රතිරෝධක රටාවක් සෑදීම සඳහා සිදු කෙරේ. පසුව ඔක්සයිඩ් පටලය හයිඩ්රොෆ්ලෝරික් අම්ලය සමඟ බෆරයක් එකතු කරන ලද අතර, HMDS ප්රතිකාරයෙන් පසුව, ප්රභා ප්රතිරෝධක රටාව වැටීමෙන් වළක්වා ගත හැකි බව සොයා ගැනේ. රූප සටහන 10 HMDS ප්රතිකාරයේ බලපෑම පෙන්වයි (රටාව ප්රමාණය 1um).
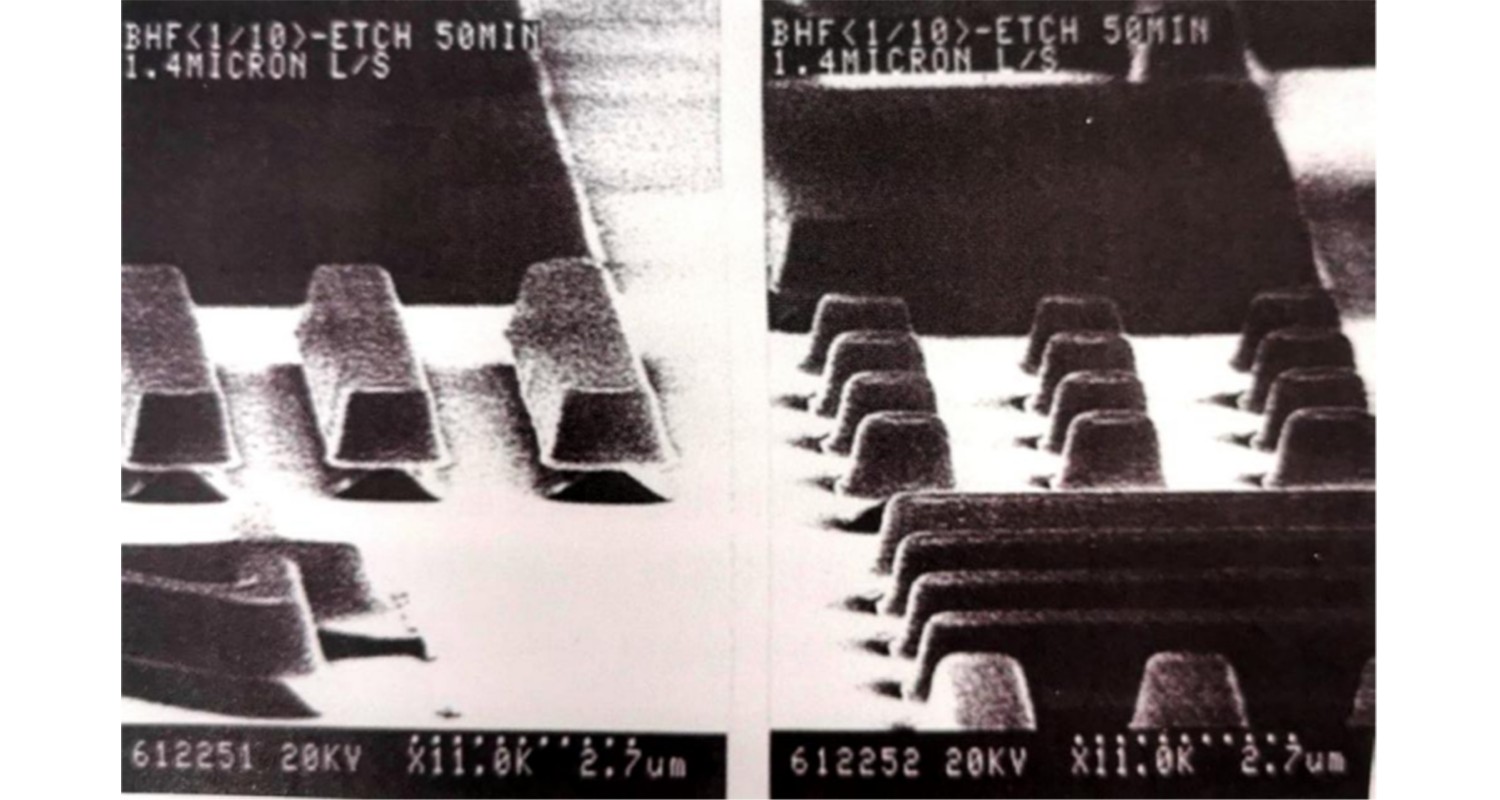
රූපය 10: HMDS ප්රතිකාර ආචරණය (රටා ප්රමාණය 1um)
පෙර පිළිස්සීම
එම භ්රමණ වේගයේ දී, පෙර පිළිස්සීමේ උෂ්ණත්වය වැඩි වන තරමට, චිත්රපටයේ ඝණකම කුඩා වන අතර, එයින් පෙන්නුම් කරන්නේ පෙර පිළිස්සීමේ උෂ්ණත්වය වැඩි වන විට, ද්රාවක වාෂ්පීකරණය වැඩි වන අතර එහි ප්රතිඵලයක් ලෙස තුනී පටල ඝණකමක් ඇති වේ. රූප සටහන 11 හි පූර්ව ෙබ්කිං උෂ්ණත්වය සහ ඩිල්ගේ A පරාමිතිය අතර සම්බන්ධය පෙන්වයි. A පරාමිතිය ඡායාරූප සංවේදී කාරකයේ සාන්ද්රණය පෙන්නුම් කරයි. රූපයෙන් පෙනෙන පරිදි, පිළිස්සීමට පෙර උෂ්ණත්වය සෙල්සියස් අංශක 140 ට වඩා වැඩි වන විට, A පරාමිතිය අඩු වන අතර, ඡායාරූප සංවේදී නියෝජිතයා මෙයට වඩා වැඩි උෂ්ණත්වයකදී දිරාපත් වන බව පෙන්නුම් කරයි. රූප සටහන 12 විවිධ පූර්ව ෙබ්කිං උෂ්ණත්වවලදී වර්ණාවලි සම්ප්රේෂණය පෙන්වයි. 160 ° C සහ 180 ° C දී, 300-500nm තරංග ආයාම පරාසය තුළ සම්ප්රේෂණය වැඩි වීමක් නිරීක්ෂණය කළ හැක. මෙම ඡායාරූප සංවේදී නියෝජිතයා ඉහළ උෂ්ණත්වවලදී පිළිස්සීම සහ දිරාපත් වන බව තහවුරු කරයි. පූර්ව ෙබ්කිං උෂ්ණත්වය ප්රශස්ත අගයක් ඇත, එය ආලෝකය ලක්ෂණ සහ සංවේදීතාව මගින් තීරණය කරනු ලැබේ.
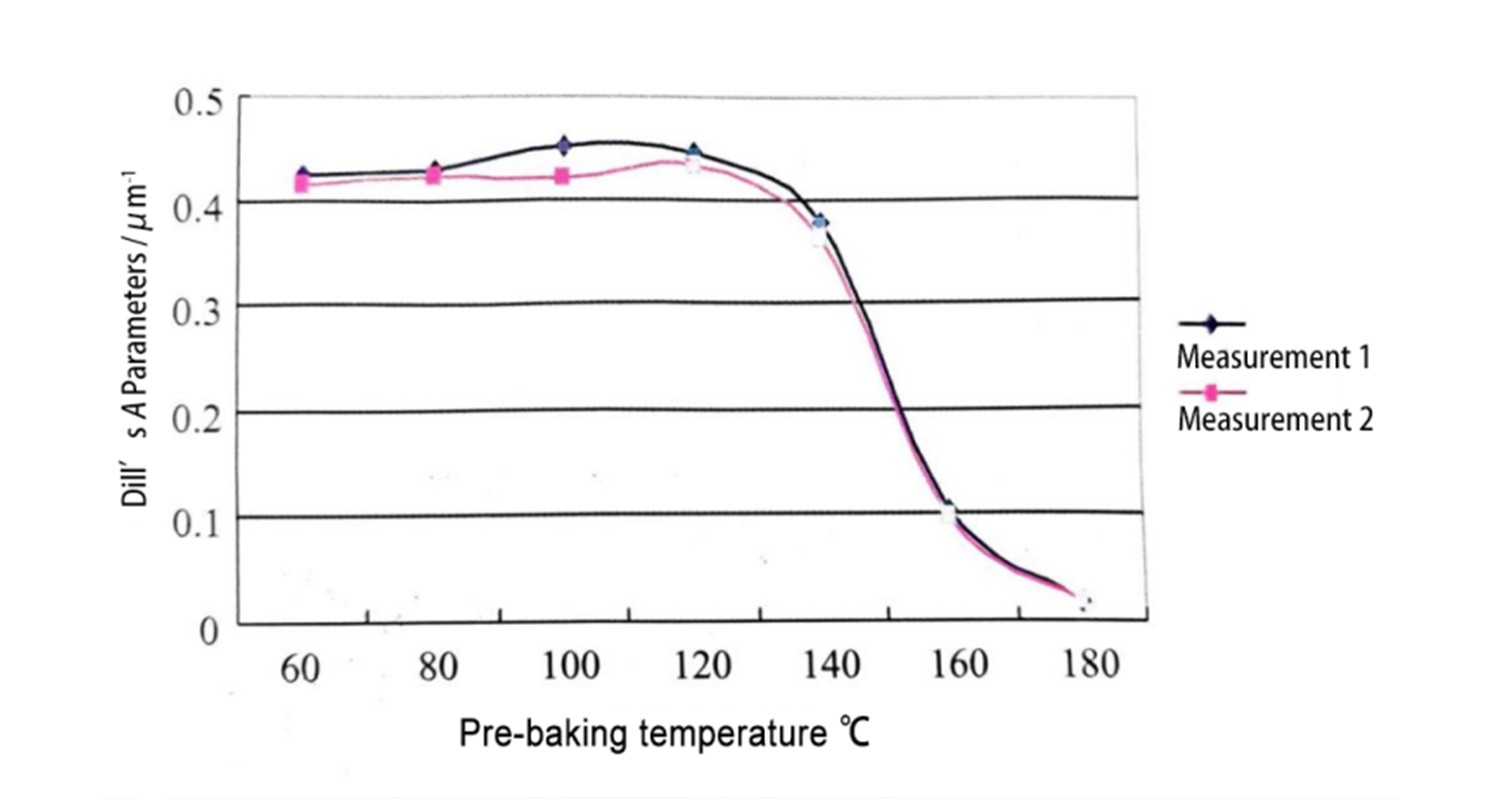
රූපය 11: පූර්ව ෙබ්කිං උෂ්ණත්වය සහ ඩිල්ගේ A පරාමිතිය අතර සම්බන්ධතාවය
(OFPR-800/2 හි මනින ලද අගය)
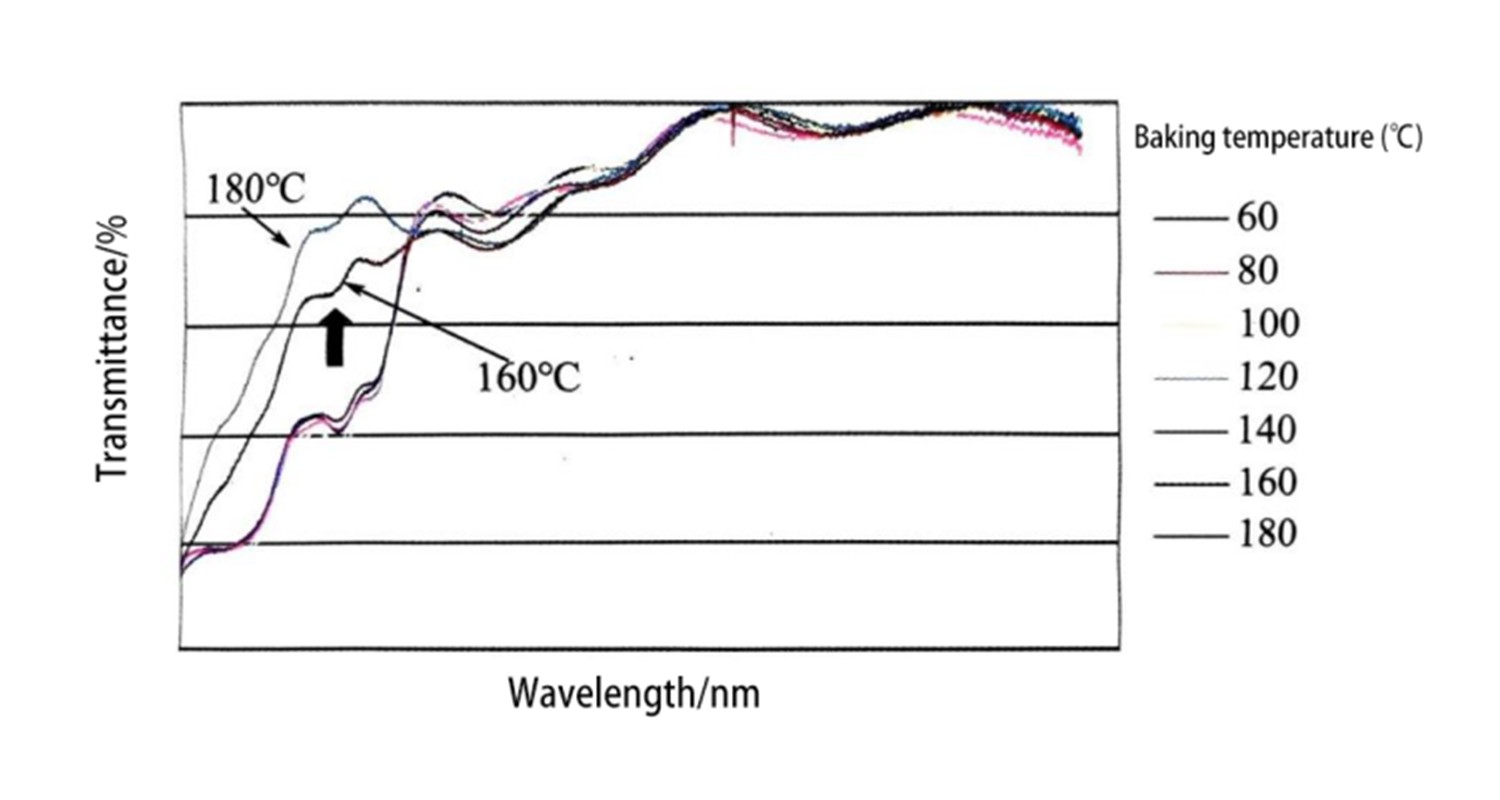
රූපය 12: විවිධ පූර්ව ෙබ්කිං උෂ්ණත්වවලදී වර්ණාවලි සම්ප්රේෂණය
(OFPR-800, 1um පටල ඝණකම)
කෙටියෙන් කිවහොත්, ස්පින් ආෙල්පන ක්රමයට චිත්රපට ඝනකම නිවැරදිව පාලනය කිරීම, අධික පිරිවැය ක්රියාකාරීත්වය, මෘදු ක්රියාවලි තත්වයන් සහ සරල ක්රියාකාරිත්වය වැනි සුවිශේෂී වාසි ඇත, එබැවින් එය දූෂණය අඩු කිරීම, බලශක්තිය ඉතිරි කිරීම සහ පිරිවැය කාර්ය සාධනය වැඩිදියුණු කිරීම සඳහා සැලකිය යුතු බලපෑමක් ඇති කරයි. මෑත වසරවලදී, ස්පින් ආලේපනය වැඩි අවධානයක් යොමු කර ඇති අතර, එහි යෙදුම ක්රමයෙන් විවිධ ක්ෂේත්ර වෙත ව්යාප්ත වී ඇත.
පසු කාලය: නොවැම්බර්-27-2024